Pneumatic Dispensers in Inhibited Layer Mode for Micro- and Mini-dosing in Forage Production
Pneumatic Dispensers in Inhibited Layer Mode for Micro- and Mini-dosing in Forage Production
Abstract
The problems occurring at mini- and micro-dosing in forage preparation are examined. It is suggested to use the equipment operating in the mode of pneumatic transporting in the mode of inhibited dense layer to solve the arising tasks. The method of calculation of such equipment is presented. Calculations showing possible costs under different technological conditions for two typical additives in fodder – dry corn gluten and lignosulphonate – have been carried out. The calculations showed the possibility of using the equipment in an inhibited dense layer as mini- and micro-dosing units with volumetric dosing of granular material. Recommendations on designing of such installations as micro- and mini-dosers are given.
1. Введение
Одним из приоритетов развития России в настоящее время является повышение эффективности сельскохозяйственного производства на основе отечественных технологий и оборудования. Достигнуть прорыва в производительности можно, учитывая особенности производства в каждом конкретном хозяйстве, для каждого поля или животного
.Рассмотрим сферу откорма животных. Во многом его эффективность связана с правильно подобранным кормовым рационом, который должен точно соответствовать породе, возрасту и состоянию животного. Поэтому в настоящее время возрастает спрос на комбикорма, вырабатываемые с учетом индивидуальных потребностей заказчика. В свою очередь это требует от производителей вводить в комбикорма большое число различных компонентов в малых дозах
. Чтобы получить желаемый эффект для каждого животного в каждой фазе его жизни необходимо добавлять компоненты в комбикорм с высочайшей точностью. Недостаточное количество ведет к уменьшению эффективности и снижению потребительских свойств всего корма. А перерасход приводит не только к потере ценных и дорогих компонентов, но и в некоторых случаях может вместо пользы принести больше вреда .В традиционных системах такое дозирование производится путем резкого уменьшения скорости подачи сыпучих компонентов. Но это приводит к тому, что последовательные процессы дозирования и смешивания многочисленных микрокомпонентов при классическом оборудовании загрузки занимают много времени.
Обычно проблема решается путем создания автоматизированного оборудования с весовым дозированием (что дороже и медленнее объёмного) и регулировкой потока сыпучего материала различными задвижками. Сам материал при этом чаще все движется самотеком (для обеспечения малой скорости), что иногда приводит к его слипанию и последующей остановке процесса.
Автоматические дозаторы представляют собой комплекс, состоящий из датчика контроля, машины-автомата для подачи и системы автоматического управления расходом. Часто такие машины объединяются в один узел по 5-8 штук для пользования единым весовым механизмом.
Существует несколько типов конструкций порошковых дозаторов, к основным из которых относятся , :
- дозаторы за счет транспортирующего газа – порошок транспортируется потоком газа (чаще всего воздуха);
- дозаторы вибрационные – порошок ссыпается в транспортирующую магистраль под действием собственной массы и вибрации;
- дозаторы шнекового типа – порошок дозируется движением шнеков, которые ссыпают порошок в приемный бункер;
- дозаторы роторного типа – порошок дозируется движением роторов, которые ссыпают порошок в приемный бункер.
Классические конструкции дозаторов имеют ряд недостатков, основные из которых – неравномерность подачи, что усложняет точное дозирование компонентов, особенно при микро- и мини-дозировании. Конструкции 2-4 типа имеют движущиеся части, что усложняет их конструкцию и управление ими. Сильное механическое воздействие на частицы может привести к их деформации и увеличенному пылеобразованию.
Управлять и регулировать пневмодозаторами гораздо проще – можно производить регулировку путем изменения потока несущего газа. Но классические пневмодозаторы имеют большую неравномерность подачи, высокие скорости движения частиц материала, малую их концентрацию на выходе из транспортной трубы. Кроме этого в отдельную проблему выливается очистка несущего газа, вместе с которым может уноситься значительное число ценных компонентов.
Но существует процесс пневмоперемещения, который лишен большинства этих недостатков – режим пневмотранспорта в заторможенном плотном слое (ЗПС). Физика процесса подробно описана в . В и описаны возможные варианты применения пневмотранспорта в ЗПС в промышленных установках.
В данной работе мы хотим исследовать возможность применения ЗПС в области подачи и дозирования компонентов в микро- и мини-объемах при производстве корма.
2. Методы и принципы исследования
Рассмотрим исследуемое оборудование. Схема дозирования с использованием ЗПС показана на рис.1 , . Вариант тормозящего устройства 5 отдельно показан на том же рисунке. Дозируемый материал поступает в питающую емкость 3 при помощи элементов 1 и 2 перед началом процесса дозирования или непрерывно в его процессе. Материал из емкости 3 за счет потока газа, поступающего в установку через патрубок 7, по трубопроводу 4 подается в конечную емкость 6. За счет тормозящего насадка 5 поток зернистого материала формируется в ЗПС. Подробнее механизм формирования и его особенности приведены в . После затормаживающего устройства 5 устанавливают перекрывающий клапан для остановки дозирования. Емкость 6 может быть оснащена весами для использования весового дозирования.
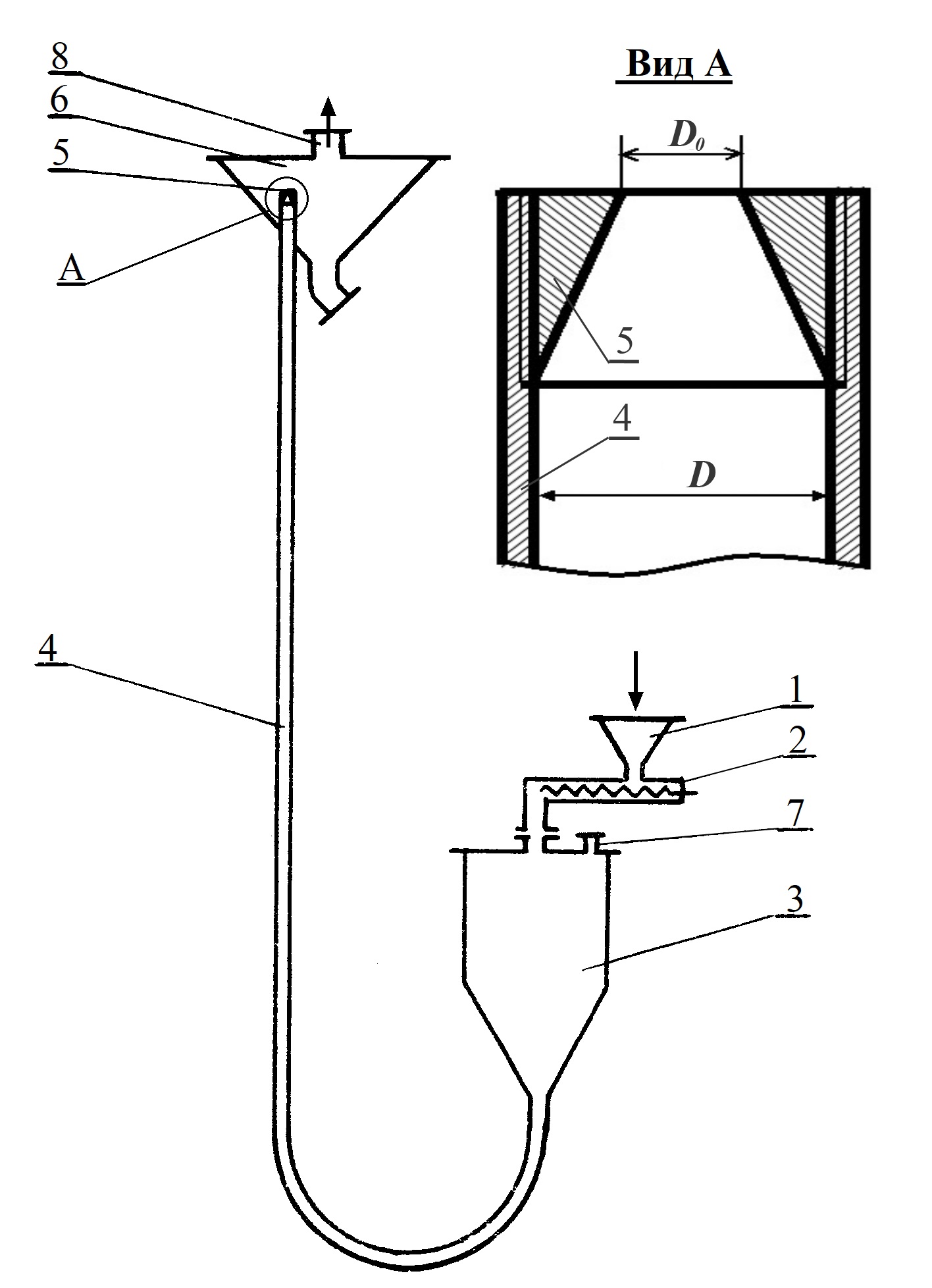
Рисунок 1 - Установка дозирования в режиме заторможенного плотного слоя
Примечание: дозируемый материал поступает в питающую емкость 3 при помощи элементов 1 и 2 перед началом процесса дозирования или непрерывно в его процессе. Материал из емкости 3 за счет потока газа, поступающего в установку через патрубок 7, по трубопроводу 4 подается в конечную емкость 6. За счет тормозящего насадка 5 поток зернистого материала формируется в ЗПС
Изучение экспериментальных данных , и наши расчеты по математической модели , показали, что в условиях пневмотранспорта в ЗПС скорость движения частиц не зависит от характеристик трубы (ее длины и шероховатости), а определяется физико-механическими свойствами зернистого материала, скоростью газа, а также размерами и формой тормозящего (сужающего) устройство 5. Это значит, что можно регулировать массовый расход дозируемого материала путем:
- подбора внутреннего диаметра трубопровода 4,
- установки степени торможения устройства 5 ,
- изменением расхода газовой фазы (изменяя давление в емкости 2).
Проверим возможности формирования малых устойчивых потоков зернистой фазы в дозаторе, реализующем ЗПС.
Для расчетов будем использовать экспериментально полученные и проверенные математическим моделированием уравнения связи средней скорости твердой фазы с технологическими параметрами пневмотранспорта в ЗПС, полученные для систем с преобладанием вертикальных труб , :
Определив соотношение средней скорости движения твердой фазы к скорости газа на выходе из транспортной трубы из уравнения (1) можно определить массовый расход зернистого материала:
В уравнение (1) учтена поправка равная 1 для тормозящего устройства, показанного на рис. 2. В случае использовании плоской шайбы правую часть уравнения (1) нужно умножить на 0,7.
Для уменьшения возможного уноса частиц с транспортным газом необходимо использовать минимально возможную скорость, которая обеспечивает надежный поток твердой фазы. В эта скорость определена как следующим образом:
Мы будем использовать в формуле (3) значение коэффициента 2,0.
На степень торможения накладывается два ограничения:
- Минимальное отношение отверстия тормозящего устройства 5 к диаметру твердой фазы не должно быть меньше 10: .
Это условие гарантирует устойчивость потока твердой фазы. Т.е. возможности минидозирования увеличиваются для более мелких порошков. Но работа при минимальной степени сжатия, особенно для относительно крупных труб и мелких порошков приводит в неоправданному увеличению начального давления транспортного газа и излишним энергетическим затратам.
- Максимально возможное торможение насадка не может быть больше чем 0,4. Увеличение этого параметра приводит к уменьшению степени торможения и переходу режима ЗПС в поршневой.
Оптимальной степенью торможения считается значение 0,3-0,35. Это позволяет получить устойчивый поток материала в трубопроводе 4 при минимальных энергетических затратах. В данной работе мы принимаем значение этого параметра 0,3.
Величина средней скорости газа зависит от разницы давлений между питающей емкостью и приемной. Этой величиной можно управлять. Однако минимально допустимой скоростью движения пневмотранспорта является скорость в два раза превышающая первую скорость псевдоожижения , .
В качестве транспортных труб будем использовать нормальный размерный ряд внутренних диаметров трубопроводом (мм): 6, 10, 15, 20, 25, 32, 40, 50, 65, 80, 100.
В качестве дозируемых материалов выберем два добавки:
- сухой кукурузный глютен (средний диаметр частиц 1,5 мм) как пример для минидозирования (до 200 кг). Коэффициент подвижности зернистого слоя примем равным 1,5 как у материала, не склонному к слипанию.
- лигносульфонат (средний диаметр частиц 100 мкм = 0,1 мм) как пример для микродозирования (до 20 кг). Коэффициент подвижности зернистого слоя примем равным 0,6 как у материала, который склонен к слипанию.
Коэффициент подвижности зернистого слоя комплексно определяет свойства зернистого слоя дозируемого материала как структуры и его возможности по псевдоожижению и пневмотранспорту (подробнее про его определение в
, ). Обычный диапазон изменения от 0,50 (слипающийся материал) до 1,6 (идеально сыпучий материал).3. Основные результаты и обсуждение
Нами произведены расчеты по описанной выше методике для дозирования сухого кукурузного глютена и лигносульфонат в режиме ЗПС.
Параметры оптимальной скорости движения газовой фазы были следующими:
- сухой кукурузный глютен;
- скорость псевдоожижения 1,775 м/с (по формуле Тодеса , );
- надежная (и рекомендуемая) скорость движения транспортного газа 3,549 м/с.
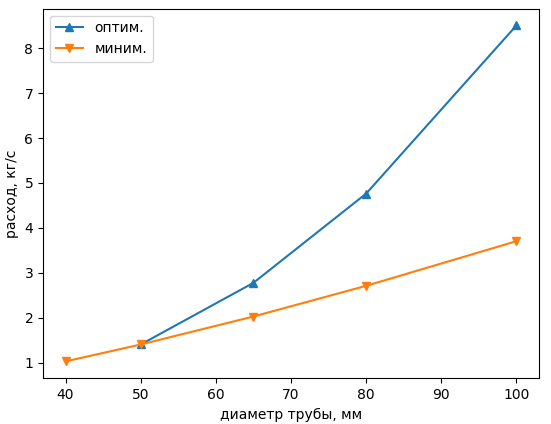
Рисунок 2 - Зависимость массового расхода зернистого материала от диаметра трубопровода (сухой кукурузный глютен) при оптимальном и минимальном сжатии
- скорость псевдоожижения 0,044 м/с (по формуле Тодеса , );
- надежная (и рекомендуемая) скорость движения транспортного газа 0,087 м/с.
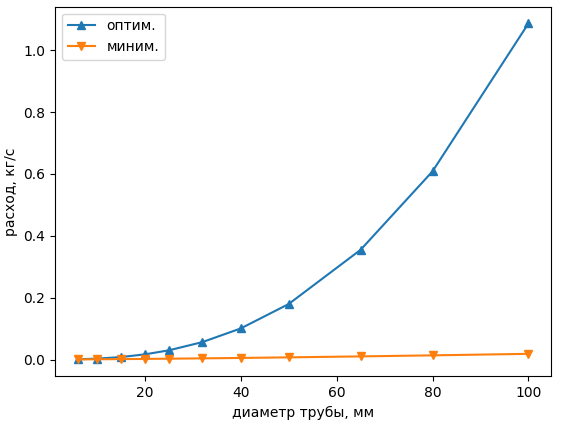
Рисунок 3 - Зависимость массового расхода зернистого материала от диаметра трубопровода (лигносульфонат) при оптимальном и минимальном сжатии
Графически расчетов представлены графически на рисунках для визуального анализа. Зависимости массового расхода дозируемого материала от диаметра транспортной трубы при оптимальных скоростях движения несущего газа представлены на рисунках 1 (глутен) и 2 (лигносульфонат). Разница в расходах твердой фазы объясняется тем, что скорость транспортного газа определялась по уравнению (3) исходя из первой скорости псевоожижения. У частиц лигносульфоната она гораздо ниже и, следовательно, ниже оптимальные скорости движения транспортного газа. Это приводит к более низким скоростям движения частиц дозируемого материала и массовым расходам.
При необходимости можно увеличивать скорости движения транспортного газа для увеличения расходов весового материала. Однако это делать не рекомендуется т.к. приведет к повышенному расходу транспортного газа и добавит сложности с его отделением от твердой фазы в емкости 6.
Увеличение разницы расходов между оптимальным и минимальным сжатиями при увеличении диаметра трубы 4 легко объяснима. При расчете минимального сжатия диаметр сжимающего устройства 5 фиксируется и при увеличении диаметра трубы только уменьшается. Для лигносульфоната степень сжатия достигает такого значения, что увеличение диаметра трубопровода уже практически перестает влиять на расходные характеристики. Также следует отметить, что энергетические расходы на дозирование при минимальных степенях сжатия сильно возрастают по сравнению с оптимальным (растет разница давлений между емкостями 3 и 6). Это обстоятельство сильно сказывается на энергетическом КПД установки.
Исходя из расходов и равномерного потока зернистого материала, можно утверждать, что мини- и микро-дозирование оборудованием, работающим в режиме ЗПС, может быть легко осуществлено с большой точностью даже объемным способом дозирования.
4. Обозначения
– средняя скорость движения зернистого материала, отнесенная к площади транспортной трубы, м/с;
– скорость псевдоожижения, м/с;
– надежная скорость движения газа по трубопроводу, м/с;
– плотность зернистого материала, кг/м3;
– плотность транспортного газа, кг/м3;
– диаметр транспортного трубопровода, м;
– диаметр выхода затормаживающего устройства, м;
– коэффициент подвижности зернистого слоя.
5. Заключение
По проведенному анализу можно сделать следующие выводы:
1. Дозаторы с движением частиц в режиме ЗПС позволяют обеспечить устойчивый поток дозируемого материала в широком диапазоне расходов как за счет подбора диаметра транспортной трубы, так и за счет подбора степени сжатия потока. Мы рекомендуем использовать подбор диаметра труб с последующей коррекцией расхода за счет скорости движения газа.
2. Устойчивый плотный поток зернистого материала позволяет проводить точное объемное дозирование, перекрывая поток дозируемого вещества по времени в конце трубопровода 4.
3. Для дозирования малых партий лучше всего подходят зернистые материалы с диаметром частиц 0,5 – 0,7 мм и менее.
4. Учитывая малый расход газовой фазы для перемещения частиц в ЗПС, можно предложить его использование для транспорта и дозирования особо ценных компонентов в среде инертных газов.